Weld Neck Flange
A weld neck flange, known for its tapered hub or high-hub design, serves a critical role in piping systems by reducing stress concentration at the base of the flange. There are two main types: one designed for pipe connections and another longer variant suitable for process plant equipment. These flanges are typically forged and welded onto pipes, ensuring robust structural integrity. The flange features a protruding round fitting that extends beyond its circumference, facilitating easy bolted connections through drilled holes on its rim. This design enhances structural stability and reliability in various applications.Long Weld Neck Flange
The long weld neck flange resembles a standard weld neck flange but is elongated, often used as a nozzle for columns or barrels. Variants like Equal LWN Barrel and LWN Heavy Barrel offer different wall thicknesses and shapes to suit specific industrial needs.Reducing Weld Neck Flange
Also known as a reducing welding neck flange, this type features a neck with a reduced diameter to weld onto smaller pipes, providing flexibility in pipeline configurations and ensuring efficient fluid flow. Weld neck flanges are essential components in piping systems, chosen for their durability, ease of installation, and ability to handle high-pressure environments effectively.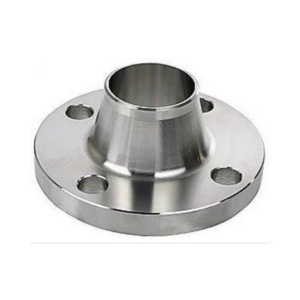
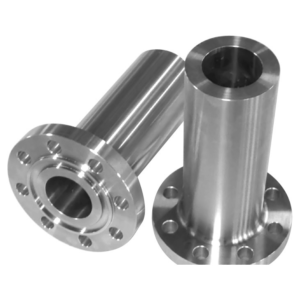
Specifications of Weld Neck Flanges
Common Outer Diameters:1/2”, 2”, 3”, 4”, 6”, 8”, 10”, 12” to 24” Special Made: Up to 60” Class Range:Class 150, 300, 400, 600, 900, 1500, 2500 (# or LB) PN (Pressure Numbers): 2.5 to 250 Flange Face Types: RF (Raised Face) RTJ (Ring Type Joint)Standards for Welding Neck (WN) Flanges:
- Material Standards:
- ASTM A105: Carbon steel welding neck flanges.
- ASTM A182: Alloy and stainless steel welding neck flanges. (Alloy includes F11, F22; Stainless includes F304/F304L, F316/F316L)
- Manufacturing Standards:
- ASME B16.5: This standard covers dimensions, tolerances, materials, marking, and testing for pipe flanges in sizes NPS 1/2 through NPS 24.
- ASME B16.47: Large diameter steel flanges (NPS 26 through NPS 60) for pressure classes 75, 150, 300, 400, 600, and 900.
- BS 3293: Specifies requirements for steel flanges for the petroleum and natural gas industries.
- DIN Standards: Includes DIN 2630 PN 1 and PN 2.5, 2631 PN 6, 2632 PN 10, 2634 PN 16, 2634 PN 25, 2635 PN 40.
Ordering Considerations:
Before ordering welding neck flanges, companies should verify:- Material Standard: Ensure compliance with ASTM A105 or ASTM A182.
- Outer Diameter: Select from standard sizes or specify special diameters up to 60”.
- Pressure Class: Choose appropriate pressure rating (e.g., Class 150, 300).
- Flange Face Type: Decide between RF or RTJ depending on application requirements.
- Thickness Schedule: Specify as per ASME B16.5 or other applicable standards.
Example Specification:
A typical description for a welding neck flange: “Flange, 10” Weld Neck, Class 150, RF, Schedule 40, ASTM A105 ASME B 16.5.”Weld Neck Flange Dimensions
NPS | Dia D | THK B | Dia A | Dia OD | Height H | Dia K | Dia L |
1/2 | 3.5 | 0.38 | 1.19 | 0.84 | 1.81 | 2.38 | 5/8 |
3/4 | 3.88 | 0.44 | 1.5 | 1.05 | 2 | 2.75 | 5/8 |
1 | 4.25 | 0.5 | 1.94 | 1.32 | 2.12 | 3.12 | 5/8 |
1.1/4 | 4.62 | 0.56 | 2.31 | 1.66 | 2.19 | 3.5 | 5/8 |
1.1/2 | 5 | 0.62 | 2.56 | 1.9 | 2.38 | 3.88 | 5/8 |
2 | 6 | 0.69 | 3.06 | 2.38 | 2.44 | 4.75 | 3/4 |
2.1/2 | 7 | 0.81 | 3.56 | 2.88 | 2.69 | 5.5 | 3/4 |
3 | 7.5 | 0.88 | 4.25 | 3.5 | 2.69 | 6 | 3/4 |
3.1/2 | 8.5 | 0.88 | 4.81 | 4 | 2.75 | 7 | 3/4 |
4 | 9 | 0.88 | 5.31 | 4.5 | 2.94 | 7.5 | 3/4 |
5 | 10 | 0.88 | 6.44 | 5.56 | 3.44 | 8.5 | 7/8 |
6 | 11 | 0.94 | 7.56 | 6.63 | 3.44 | 9.5 | 7/8 |
8 | 13.5 | 1.06 | 9.69 | 8.63 | 3.94 | 11.75 | 7/8 |
10 | 16 | 1.12 | 12 | 10.75 | 3.94 | 14.25 | 1 |
12 | 19 | 1.19 | 14.38 | 12.75 | 4.44 | 17 | 1 |
14 | 21 | 1.31 | 15.75 | 14 | 4.94 | 18.75 | 1.1/8 |
16 | 23.5 | 1.38 | 18 | 16 | 4.94 | 21.25 | 1.1/8 |
18 | 25 | 1.5 | 19.88 | 18 | 5.44 | 22.75 | 1.1/4 |
20 | 27.5 | 1.62 | 22 | 20 | 5.62 | 25 | 1.1/4 |
24 | 32 | 1.81 | 26.12 | 24 | 5.94 | 29.5 | 1.3/8 |
6” Weld Neck Flange Class 150 and 300 Dimensions and Weight
Class 150 WN Flange in 6 inch (Raised Face) Weight 10.94 KG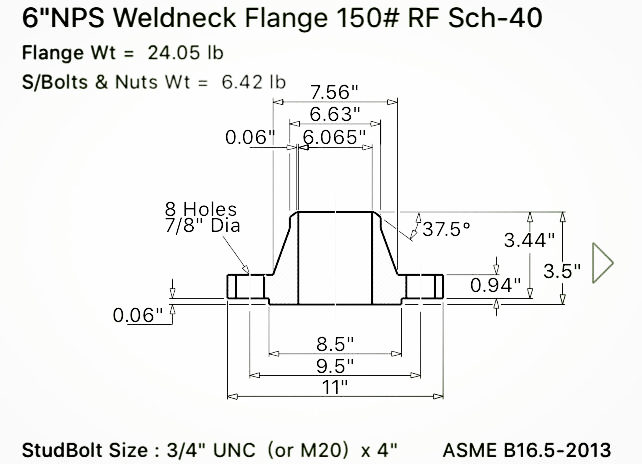
FAQs
What size are weld neck flanges?
Weld neck flanges are designed to match the inside diameter of pipes, making them suitable for high-pressure applications. These flanges typically range in size from 1/2″ to 96″, covering a wide spectrum of pipe diameters to ensure compatibility and strength in various industrial settings. This range allows weld neck flanges to accommodate different pipe sizes and pressures effectively, meeting the requirements of diverse piping systems and applications.
What is the dimension standard for flanges?
The dimension standard for flanges, as per ASME B16.5, dictates bolt hole sizes like 12 x 25.4mm Class 150, 16 x 32mm Class 300, ensuring standardized compatibility.
What is a welded flange?
A weld neck flange features a long tapered hub designed to smoothly transition to the pipe or fitting it connects to. It’s commonly butt-welded to the line by inserting the pipe end into the flange and welding it around the circumference. This method ensures a robust and secure joint, minimizing the risk of leaks.