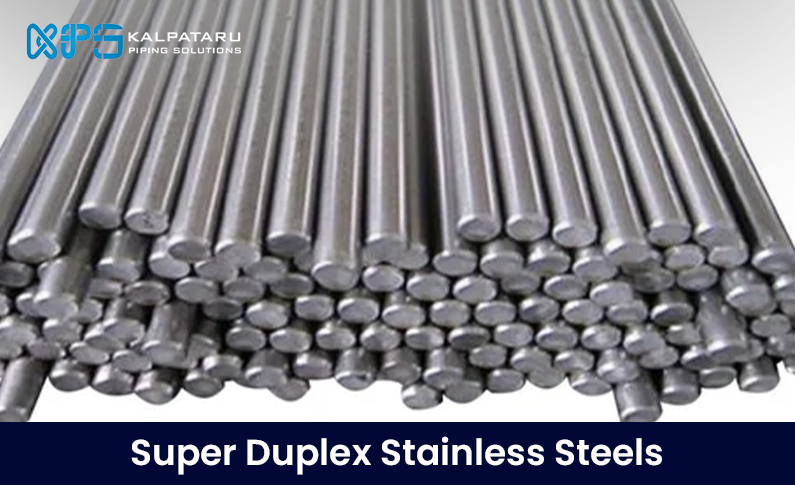
SAE 1045 Carbon Steel – Chemical Composition, Properties and Uses
SAE 1045/AISI 1045 Carbon Steel is a medium-carbon steel known for its excellent combination of strength, machinability, and toughness. This material offers good weldability, allowing for easy fabrication and joining in various industrial applications. It also possesses high impact resistance, making it suitable for demanding environments.
SAE 1045/AISI 1045 steel is commonly used in the production of critical components such as axles, bolts, forged connecting rods, crankshafts, and torsion bars. These applications benefit from its high strength and durability, ensuring reliability under heavy loads and stress conditions. The material’s good machinability also facilitates efficient manufacturing processes, reducing production costs.
In addition to its use in automotive and mechanical components, SAE 1045/AISI 1045 steel is also employed in the manufacturing of light gears, guide rods, and other machinery parts. Its versatile properties make it a popular choice in industries such as automotive, construction, and engineering, where strength, toughness, and performance are essential.
What does 1045 mean in steel?
In steel identification, “1045” refers to the specific grade of steel classified by the American Iron and Steel Institute (AISI) and the Society of Automotive Engineers (SAE).
AISI/SAE Classification:
The first digit “1” in 1045 indicates that the steel is primarily a carbon steel.
The second digit “0” shows that the steel does not contain significant alloying elements, classifying it as a plain carbon steel.
Carbon Content:
The final two digits “45” represent the steel’s carbon content, which is 0.45%. This carbon content gives the steel its strength, hardness, and other key mechanical properties.
1045 steel is widely used in applications where good strength, machinability, and toughness are required, such as axles, bolts, connecting rods, crankshafts, and other mechanical components.
Chemical Composition of 1045 Carbon Steel
Grade | C | Si | Mn | P | S |
1045 | 0.43-0.50 | 0.15-0.35 | 0.60-0.90 | ≤0.04 | ≤0.05 |
SAE 1045 Steel Physical Property
Density, g/cm3 | 7.86 |
Melting point,℃ | 1433 |
Specific heat capacity,(0~100℃),J/(kg.k) | 577.78(200℃) |
Linear expansion coefficient,10^-6/k | 0~100℃ |
11.7 | |
Poisson’s ratio | 0.269 |
Elastic Modulus,Mpa | 209000 |
Shear modulus,Mpa | 82300 |
Thermal conductivity,W/(m.K) | 46.89(200℃) |
Resistivity,10^-8 Ω.m | 32.0(200℃) |
SAE 1045 Mechanical Property
Tensile,Mpa | Yield,Mpa | Elongation,% | Reduction,% | Charpy Impact,J | Hardness,HBW |
≥532 | ≥280 | ≥32 | ≥49 | ≥60 | 160-200 |
SAE 1045 Thermal Properties
Properties | Metric | Imperial |
Thermal conductivity | 51.9 W/mK | 360 BTU in/hr.ft2.°F |
Thermal expansion co-efficient (@0.000-100°C/32-212°F) | 11.2 µm/m°C | 6.22 µm/m°C |
Advantages of Using 1045 Carbon Steel
Using 1045 carbon steel offers several key advantages:
- High Tensile Strength and Hardness: 1045 carbon steel provides excellent tensile strength and hardness, making it ideal for applications that require durability and toughness.
- Ease of Machining: Its relatively low carbon content allows 1045 steel to be easily machined into various shapes and forms, ensuring efficient manufacturing processes.
- Weldability: 1045 carbon steel is suitable for welding, making it versatile for various industrial applications. Proper welding techniques can ensure strong and reliable joints.
- Wear Resistance: The microstructure of 1045 steel, which consists of ferrite and pearlite, enhances its wear resistance. The pearlite structure, containing carbides, contributes to improved wear resistance, making it suitable for parts exposed to friction and wear.
Disadvantages of Using 1045 Carbon Steel
While 1045 carbon steel has many advantages, there are some limitations to consider:
- Poor Corrosion Resistance: 1045 steel is not highly resistant to corrosion, particularly in harsh environments. It may require additional protective coatings or regular maintenance to prevent corrosion.
- Limited Hardenability: This steel grade has a lower ability to be hardened through heat treatment compared to other steel types. This limits its suitability for applications that require high hardness or wear resistance.
- Heat Treatment and Welding Challenges: Improper heat treatment or welding techniques can lead to cracking or distortion in 1045 carbon steel components, reducing their structural integrity.
- Higher Cost Compared to Lower-Grade Steels: Although 1045 carbon steel is not classified as high-cost, it tends to be more expensive than lower-grade carbon steels. Costs can vary based on factors like quality, availability, and specific project requirements.
Difference Between 1045 Carbon Steel and A514 Steel
The main difference between 1045 carbon steel and A514 steel (T1) is their composition and strength. A514 is a high-strength, low-alloy steel with added elements like chromium, manganese, and carbon, making it ideal for structural applications that require greater strength and hardness. In contrast, 1045 carbon steel, with 0.45% carbon content, is a medium-carbon steel commonly used for general-purpose applications due to its good strength and versatility.
Conclusion
SAE 1045 steel is a widely used and versatile medium-carbon steel known for its strong balance of strength, machinability, and impact resistance. Its affordability and adaptability make it a preferred choice for applications such as axles, gears, shafts, and more. Whether in a hot-rolled or normalized condition, SAE 1045 delivers reliable performance in demanding environments. The steel’s ability to be heat-treated further enhances its mechanical properties, ensuring it meets the needs of various industries. In conclusion, SAE 1045 offers a cost-effective and practical solution for a wide range of engineering applications, making it a valuable material in many industrial sectors.
FAQs
What is 1045 carbon steel used for?
1045 carbon steel, known for its medium tensile strength and machinability, is commonly used in machinery parts, gears, crankshafts, shafts, axles, bolts, studs, and support plates.
What grade of steel is 1045?
1045 steel is a medium-carbon common steel grade, valued for its moderate weldability, higher strength, and impact properties, making it versatile and cost-effective for various applications.
What is SAE 1045?
SAE 1045 is a medium-carbon steel known for its high strength, weldability, and impact resistance, making it a versatile and widely used material globally.